BILL Helps give Arizona Auto Parts a back office tune-up with AP Automation
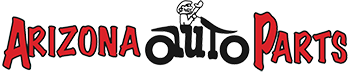
Customer
Established in 1919, with over 100 years in the recycled auto parts business, Arizona Auto Parts provides trusted, premium, rust-free recycled parts for the western United States and northern Mexico.
# of employees
300+
Industry
Reused & Recycled Auto Parts
Challenge
To expand operations and increase vehicle purchases to meet rapidly rising demand, without adding to head count or working hours.
Solution
BILL
Accounting software integration
NetSuite
Results
About 11 million cars are scrapped every year in the U.S. Imagine filling every square inch of 275 football stadiums with an automotive graveyard of ‘48 Chevys, VW buses, and ‘80s Suburbans every year. In terms of environmental impact, this is obviously a huge problem. But it’s here that Arizona Auto Parts found a huge opportunity.
“Fortunately, only about 5% of that has to be discarded,” said Kristopher Houchin, Controller for Arizona Auto Parts. “Approximately 70% of each vehicle can be reused. Those are sellable parts. Another 25% can be recycled. We’ve been reusing and recycling America’s auto parts since 1919. We were green before being green was even a thing.”
Over the past century, what started as a single family-owned junkyard has become big business, with an online searchable parts inventory that ships across the country.
“We have 9 locations, 3 recycling yards, and more than 300 employees across some 20-odd companies, all of which are set up in BILL to flow seamlessly into NetSuite,” Houchin told us.
“We work with car dealerships. Body shops. Individual people. We buy cars off the street and we buy them at auction,” said Houchin.
“We run thousands of transactions every month, all with a back-office staff of only 7 accountants. Without BILL, we couldn’t do it. We just couldn’t.” — Kristopher Houchin, Controller, Arizona Auto Parts
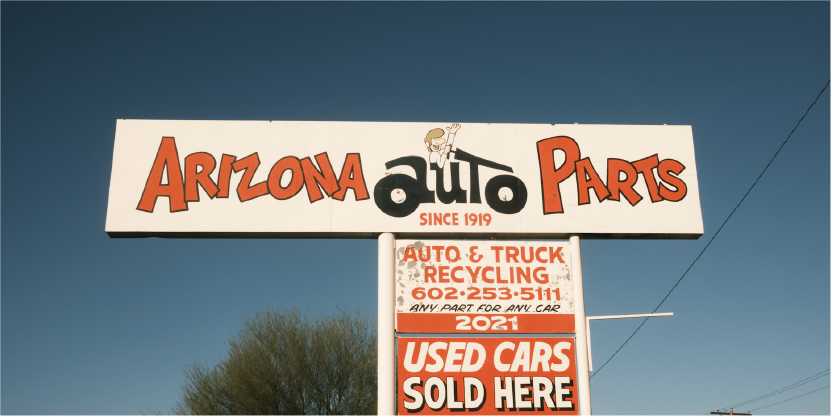
Physical checks were a roadblock to growth
Houchin started with Arizona Auto Parts in 2019. He remembers all too well what it was like to keep up with day-to-day operations by cutting physical checks.
“It’s an interesting line of business,” he said. “We don’t manufacture anything. We buy and we sell. Inventory changes constantly. We have to keep scrapped cars coming in, but cutting hundreds of checks every week and mailing them is a hassle. BILL was an easy sell for us.”
From the time Arizona Auto Parts first opened its doors, it wrote up every deal individually. Even as the company expanded, eventually moving to modern, enterprise-level accounting software, the team was still managing purchase deals and payments by hand.
As Houchin notes: “There was no defined process. We wrote checks for everything—sometimes before invoices were in the system to make sure payments went out on time. Others might sit on someone’s desk for weeks because we didn’t need to send them yet. There were plenty of horror stories. Lost checks. Checks needing to be voided and recut. It was a real waste of time and resources.”
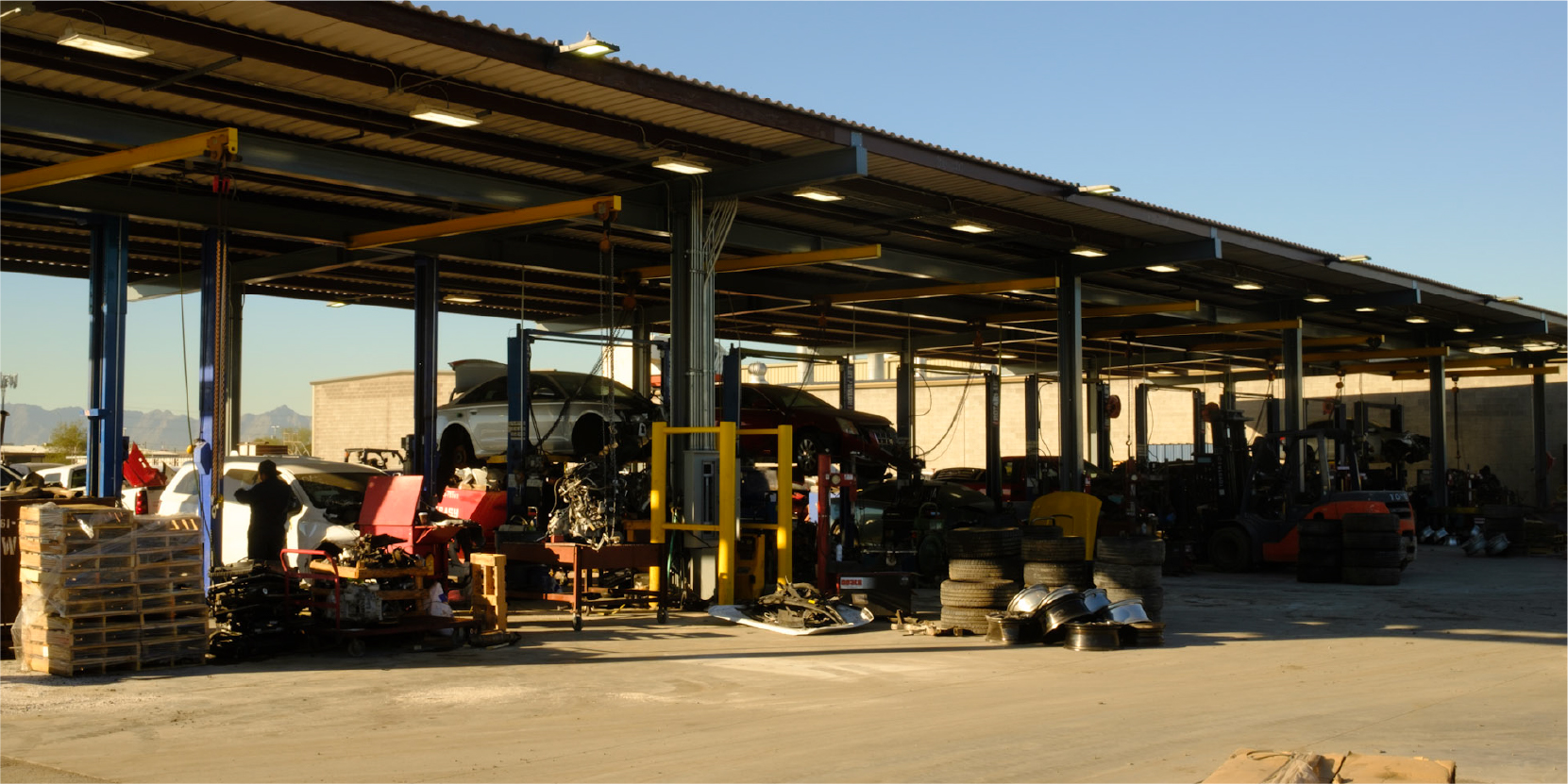
Road trip—Arizona Auto Parts goes looking for an AP solution that integrates with NetSuite
Filling out hundreds of checks every month impacted the whole accounting team, not to mention the CFO, Russell Sewell, and the company’s president, Mike Pierson, who was “at his desk until 7 p.m. almost every night signing checks,” according to Houchin.
Because the company was already working with Oracle NetSuite, Sewell attended SuiteWorld hoping to find something that could help them streamline and standardize their payments process.
“BILL was there,” Houchin told us. “We checked it out and asked a lot of questions. Did it integrate with NetSuite? Absolutely. Would it work with all our entities while keeping them separate from each other? Yes. Could it handle the sheer volume of checks we were writing? Definitely. Plus, it could scale with us as we grew.”
When Arizona Auto Parts added BILL to its tech stack, Houchin called the results “amazing.”
“After 2 years of operations, I can’t speak more highly of the BILL and NetSuite integration. It eliminated our manual processes. Everything is so much easier with BILL and NetSuite together.” — Kristopher Houchin, Controller, Arizona Auto Parts
BILL accelerates their payables—and their growth
Why is that integration so important for Arizona Auto Parts? Houchin explained.
“We have a standard process now. The AI in BILL reads each invoice and enters the data. All we have to do is click ‘Okay’ to approve it and send the payment on its way. Those transactions automatically flow into NetSuite, keeping our books up to date.”
The streamlined integration saves the company time in more ways than one.
“Thanks to BILL, we’ve reduced the time we spend on payables by at least 25%.” — Kristopher Houchin, Controller, Arizona Auto Parts
“We can pay people much more quickly using ACH. We don’t need to chase down checks, searching through stacks and stacks of paper. For the last 3 stores we opened, I was even able to set them up on my own.”
One of the biggest improvements Houchin has seen is in their monthly close.
“When a check sits on a desk, your books don’t reconcile,” he commented. “You have to figure it all out. Where’s this? Where’s that? We used to close on the 20th of the month. Now we close on the 7th. I wouldn’t even be talking to you right now if this was before we used BILL. I’d be working on our close. BILL has been a life saver. It’s worth its weight in gold.”
And there was one more improvement that had Houchin smiling.
“The accounting group sits right around the corner from my office, sharing the space with 6 or 7 big filing cabinets. Recently, it hit me, ‘Do we even use these anymore?’ We looked through them, and the only things in there were old invoices and check copies that are in BILL now. So we got rid of them. With all that extra space, it’s a much nicer place to work in.”
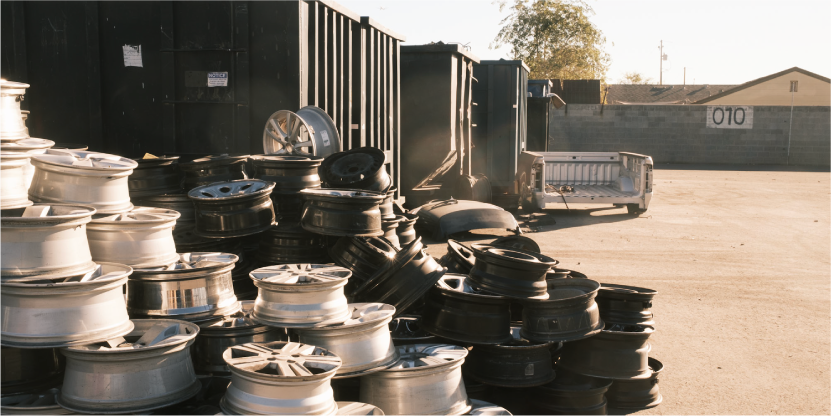
What’s next—keeping America’s wheels on the road
The company has long benefited from the Arizona weather. With no road salt in the winter and very little rain, Arizona Auto Parts offers a bounty of rust-free parts to the rest of the country. Recently, that mission has taken a more serious turn.
According to Houchin, “With supply chain issues making it harder for people to purchase new cars, we’ve seen a real upturn in demand. People need us more than ever, and we’re going to be there for them. We’re doing everything we can to keep America running.”
That’s the way Arizona Auto Parts has always been, coming through not just for their customers, but for each other.
“It’s the epitome of a family-owned business,” Houchin said. “People get a job with us and stay until they retire. Often 30 years or more. We work hard, but we’re also encouraged to go home at a reasonable hour. To spend time with our families. Technology like BILL is a big piece of that. When you can use tech to expand without working longer hours, so you can still have a life outside of work, that’s the best kind of family business there is.”
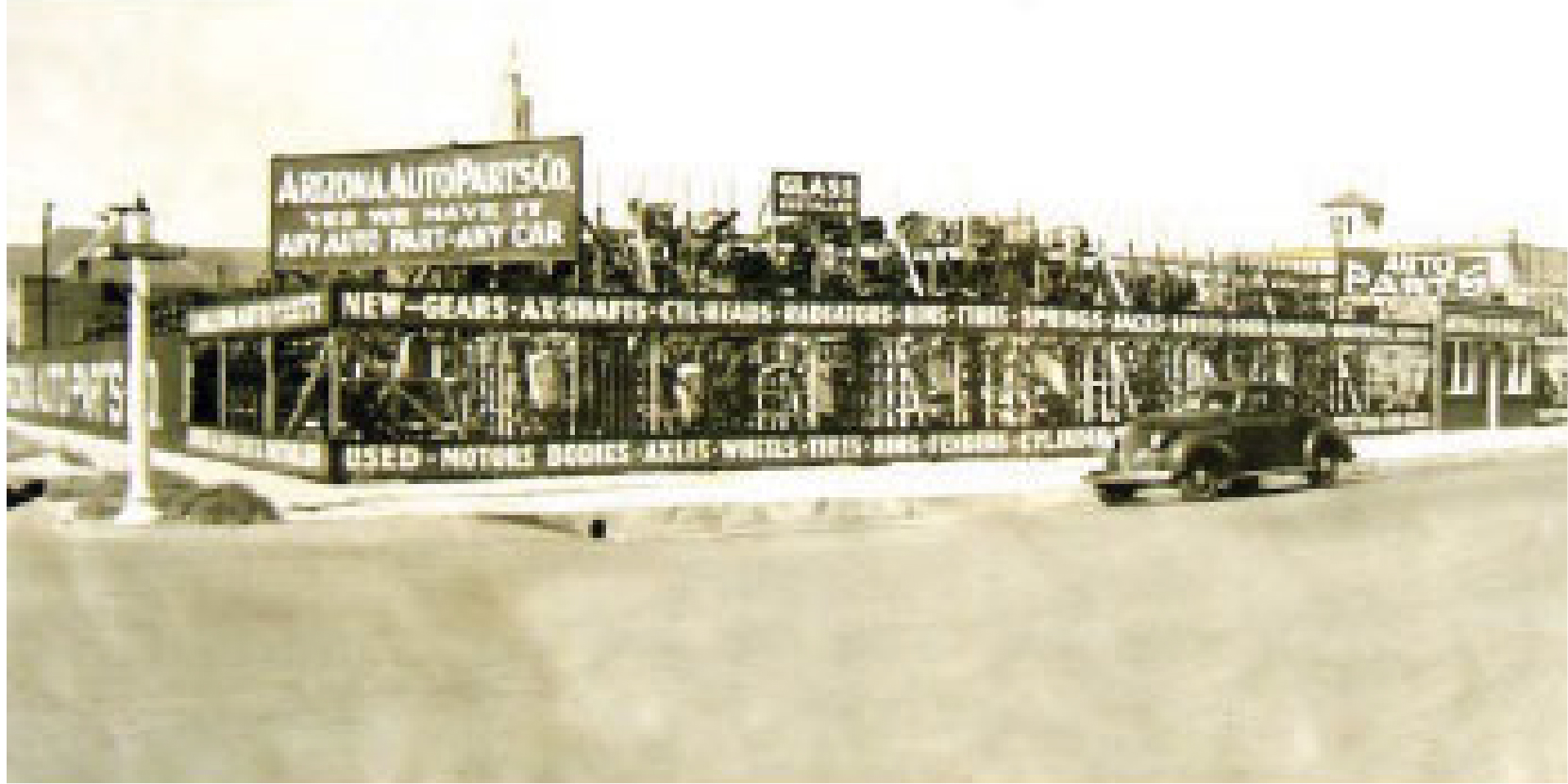
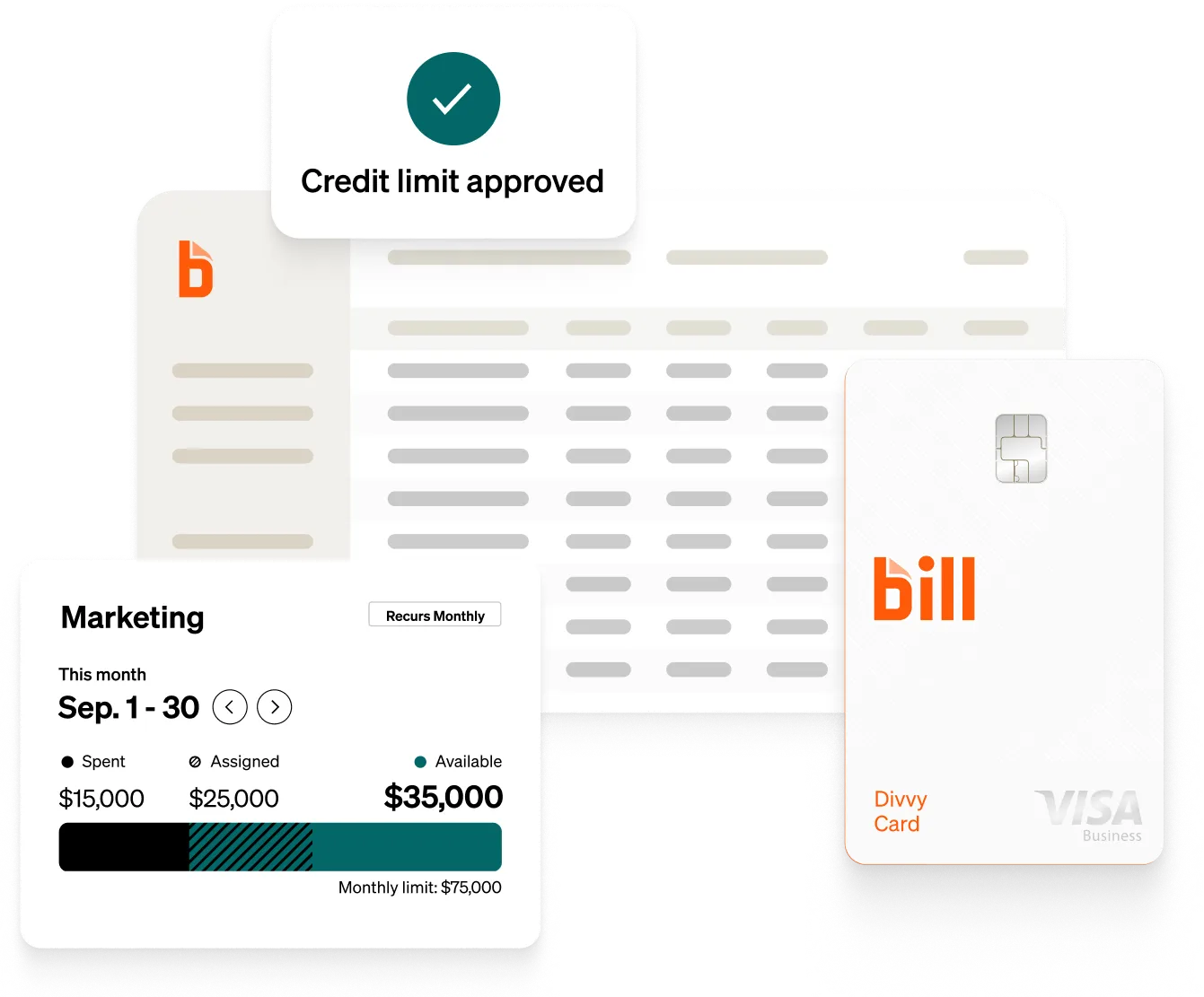
Ready to bring AI to your finance team?
Take a demo with BILL to see how our integrated platform can provide your business with seamless AP, AR, and spend and expense management.